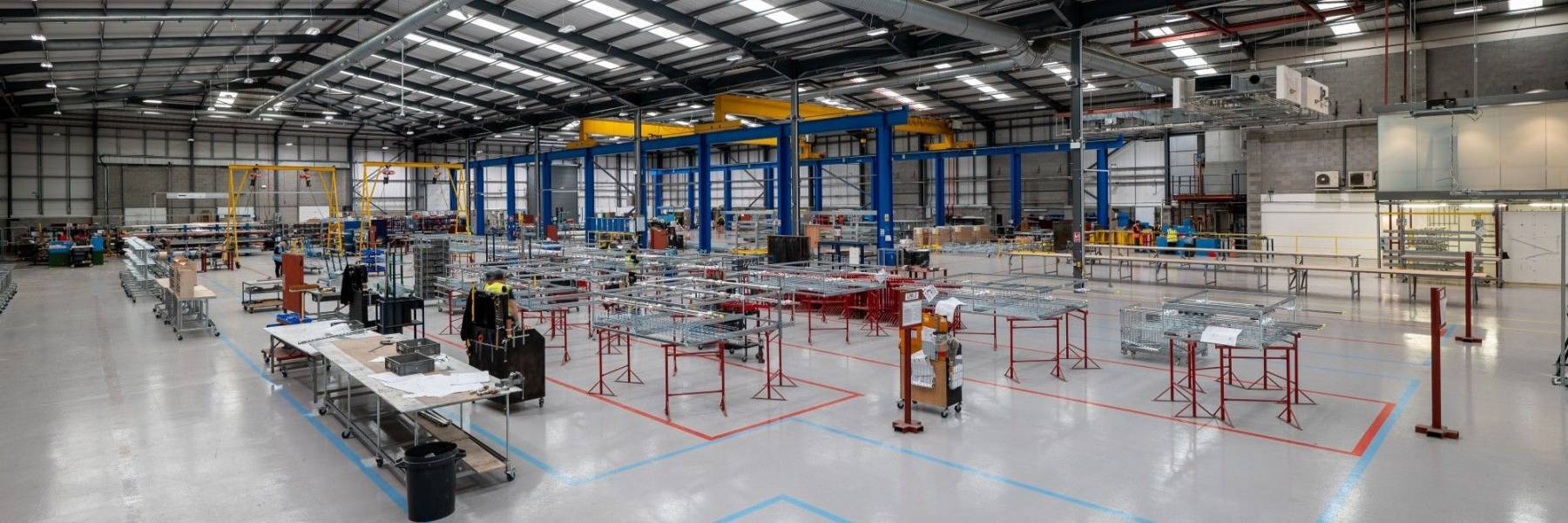
What is offsite manufacturing?
At NG Bailey, we’ve been proud advocates of offsite manufacturing for over two decades, with a well-deserved reputation as experts in this area.
Offsite Manufacture and its use within the construction sector has evolved, with a greater emphasis on the benefits it brings to our industry, the wider environment and our business operations. By utilising offsite manufacturing techniques it makes construction more sustainable increases productivity, improves quality, delivers certainty on programme and costs, and dramatically reduces health and safety risks.
Ultimately Offsite Manufacture is Safer, Better, Faster and Greener!
View our full range of standard products
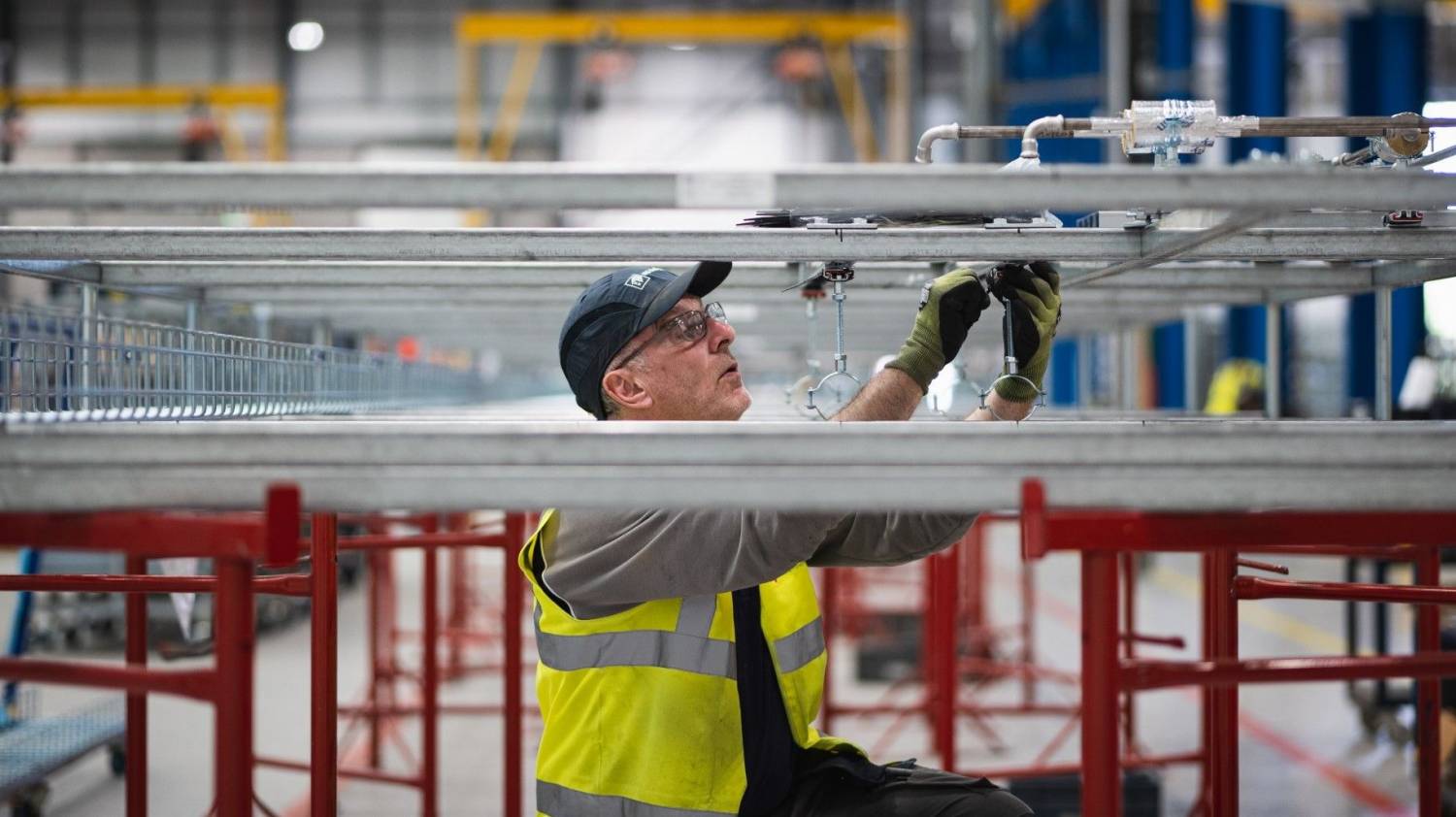
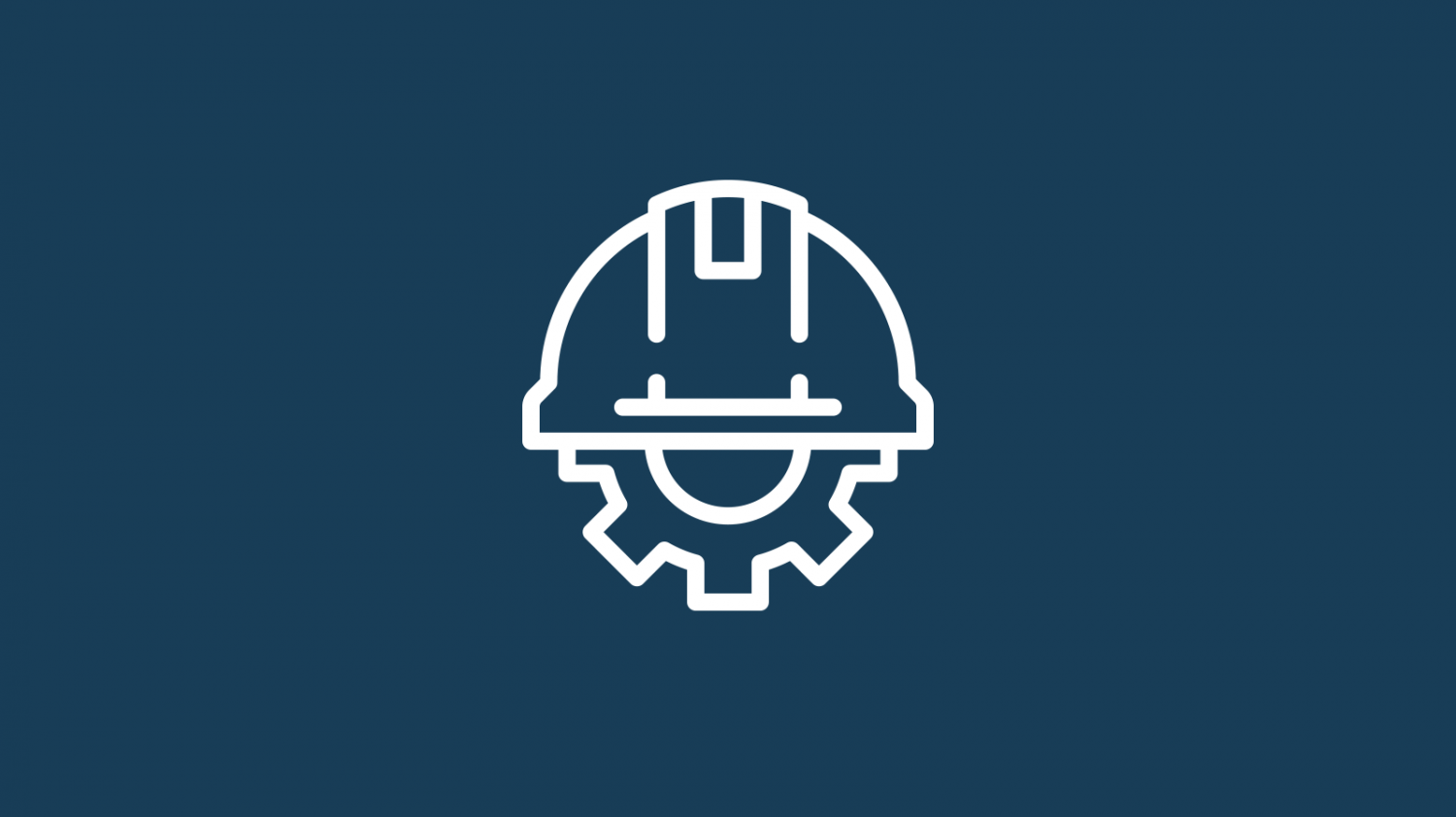
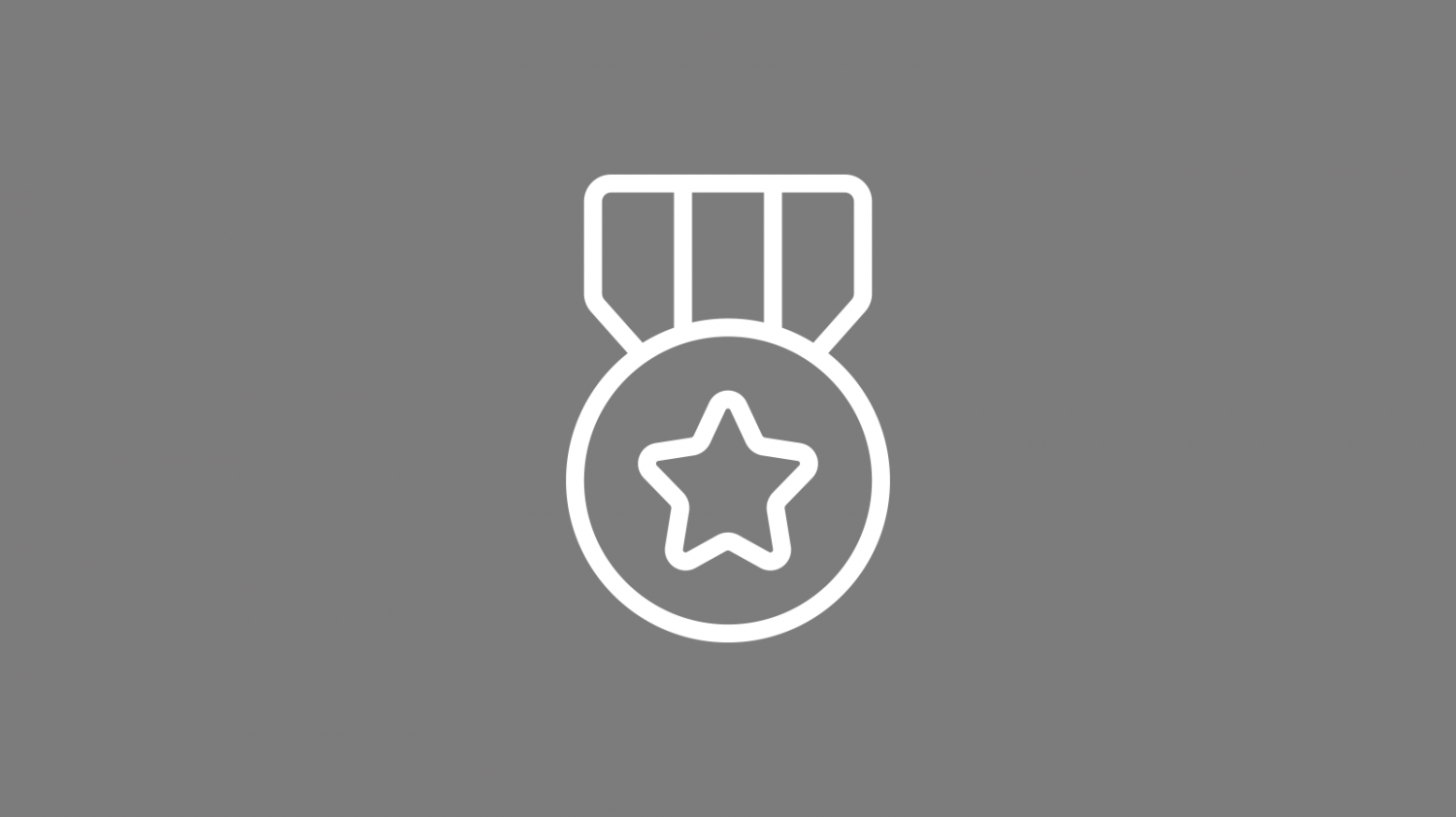
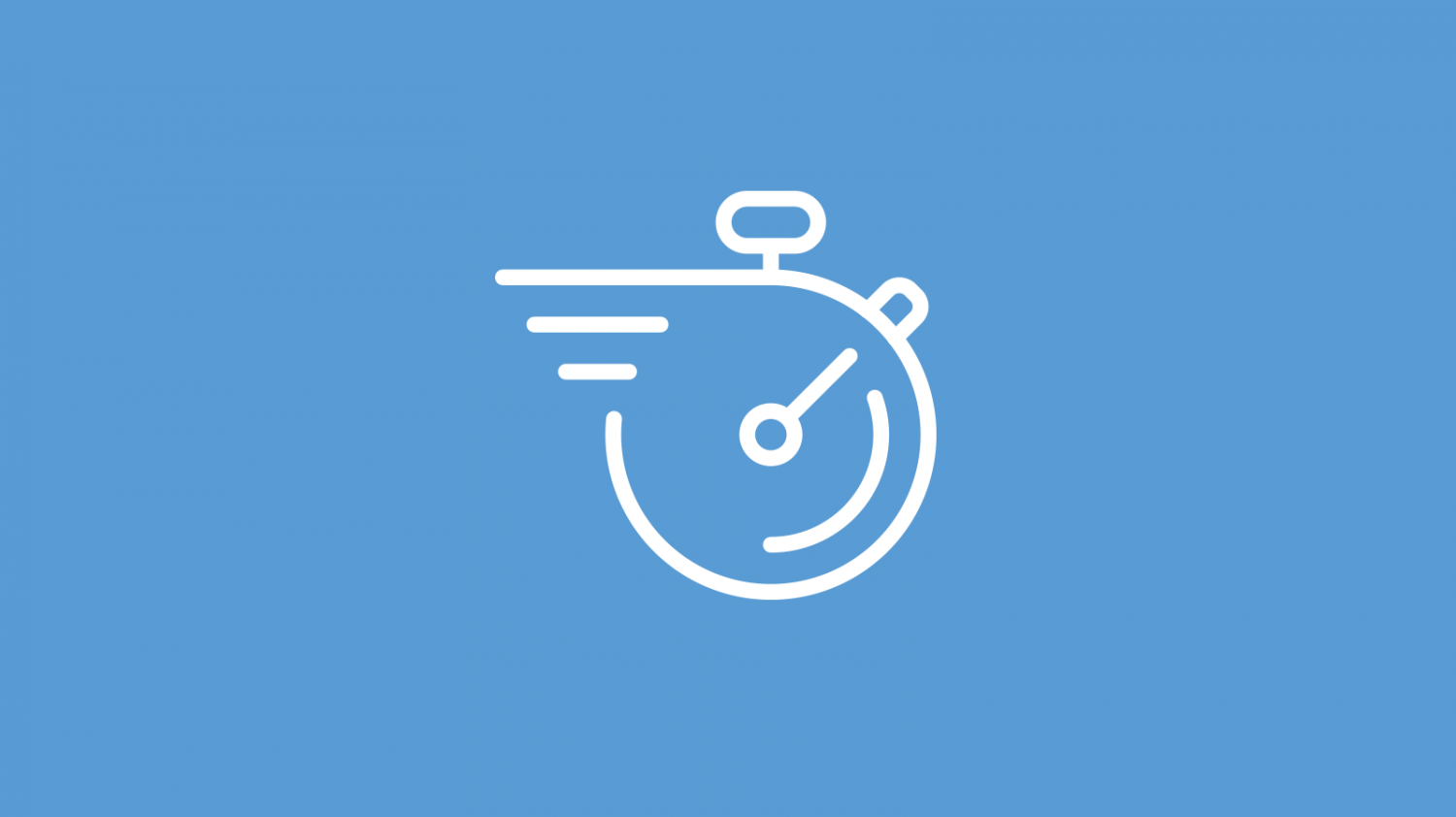
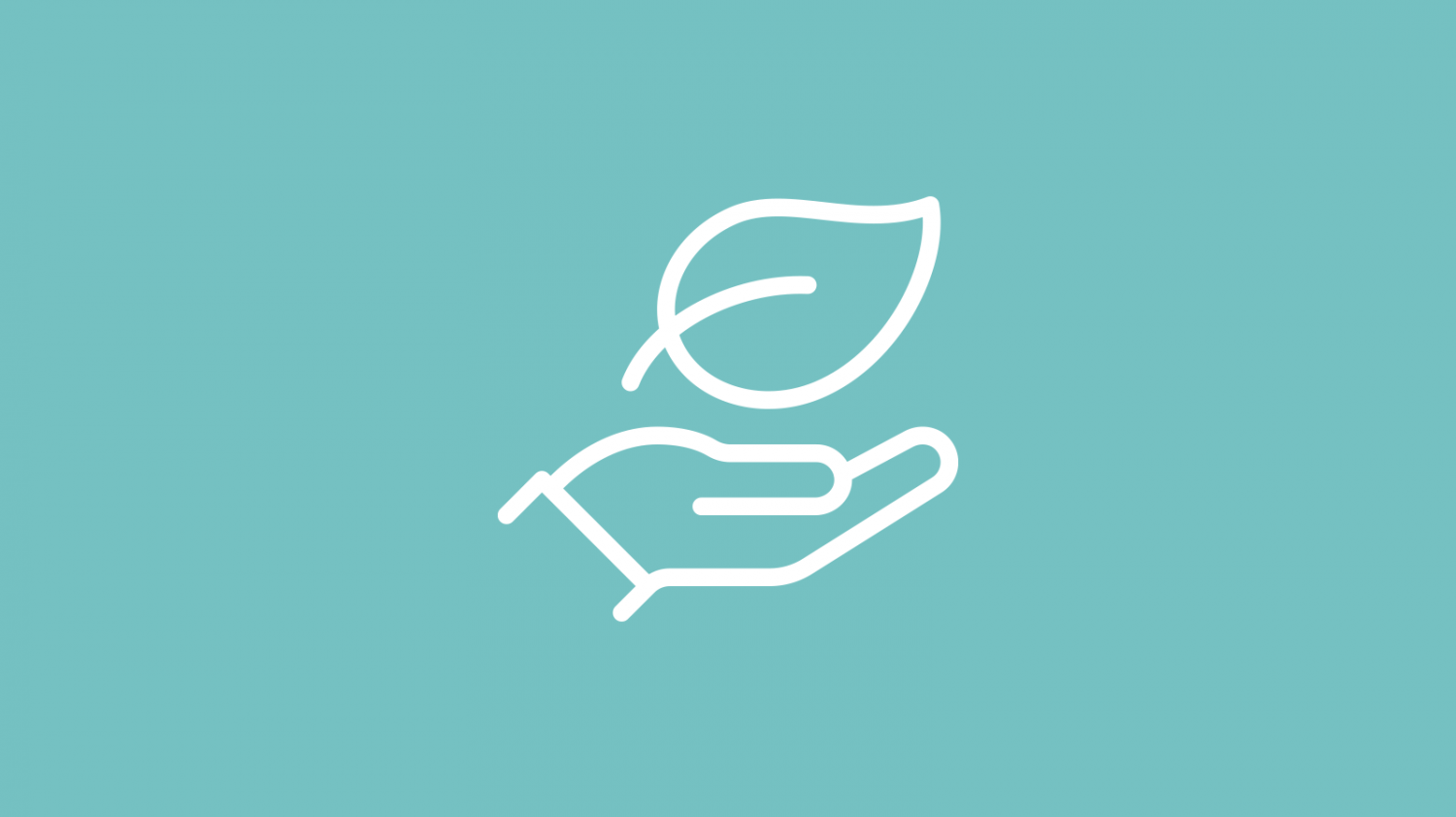
Safer
The construction industry has the highest number of accidents in the UK. Working at height, manual handling, lifting heavy loads and the presence of live machinery all contribute to the risks. Offsite Manufacture is a safe, predictable setting unaffected by variable weather and visibility.
Better
The future of offsite manufacturing is changing and we are in a strong position to help lead this transformation. Offsite Manufacture improves productivity, drives collaboration with partners and increases quality assurance.
Faster
Assembly at Offsite Manufacture provides certainty of programme delivery. By manufacturing components offsite, they can be produced and quality checked in readiness for delivery to site and installation. Installation is then a much faster, simpler and safer process.
Greener
Our Offsite Manufacturing facility is powered from renewable and sustainable sources, we generate our own solar energy which has already saved more than 262 tonnes of carbon – equivalent to 4332 trees seedlings grown for 10 years, or the annual energy use of 48 homes.
Offsite manufacturing benefits
Our vision is to achieve a World Class Manufacturing (WCM) status
WCM methodology focuses on management principles linked to Safety, Cost, Quality Control, Logistics, Customer Service, People Development & Environment, all with direct synergy with the NG Bailey DNA.
Each of these pillars demonstrates the Value of Modern Methods of Construction (MMC). Through Effective engagement with the broader business, the NG Bailey Manufacturing Facility will ensure that these benefits are understood, enabling our teams to integrate solutions efficiently into project delivery whilst maximising our ability to sell the value to our customers.
People drive success; within the team in this business, there is a real focus at both facilities to deliver quality solutions consistently. The challenge now is to invest in this model, ensuring the tools and processes are in place to ensure NG Bailey Offsite Manufacturing remains at the forefront of the M&E sector with its Manufacturing capability.
Over the next two years, the Oakenshaw and Driglington facilities have got a clear investment strategy to ensure they become facilities that exhibit the commitment of the NG Bailey group in delivering World Class Manufacturing as standard with a focus on enhancing capability in this space.
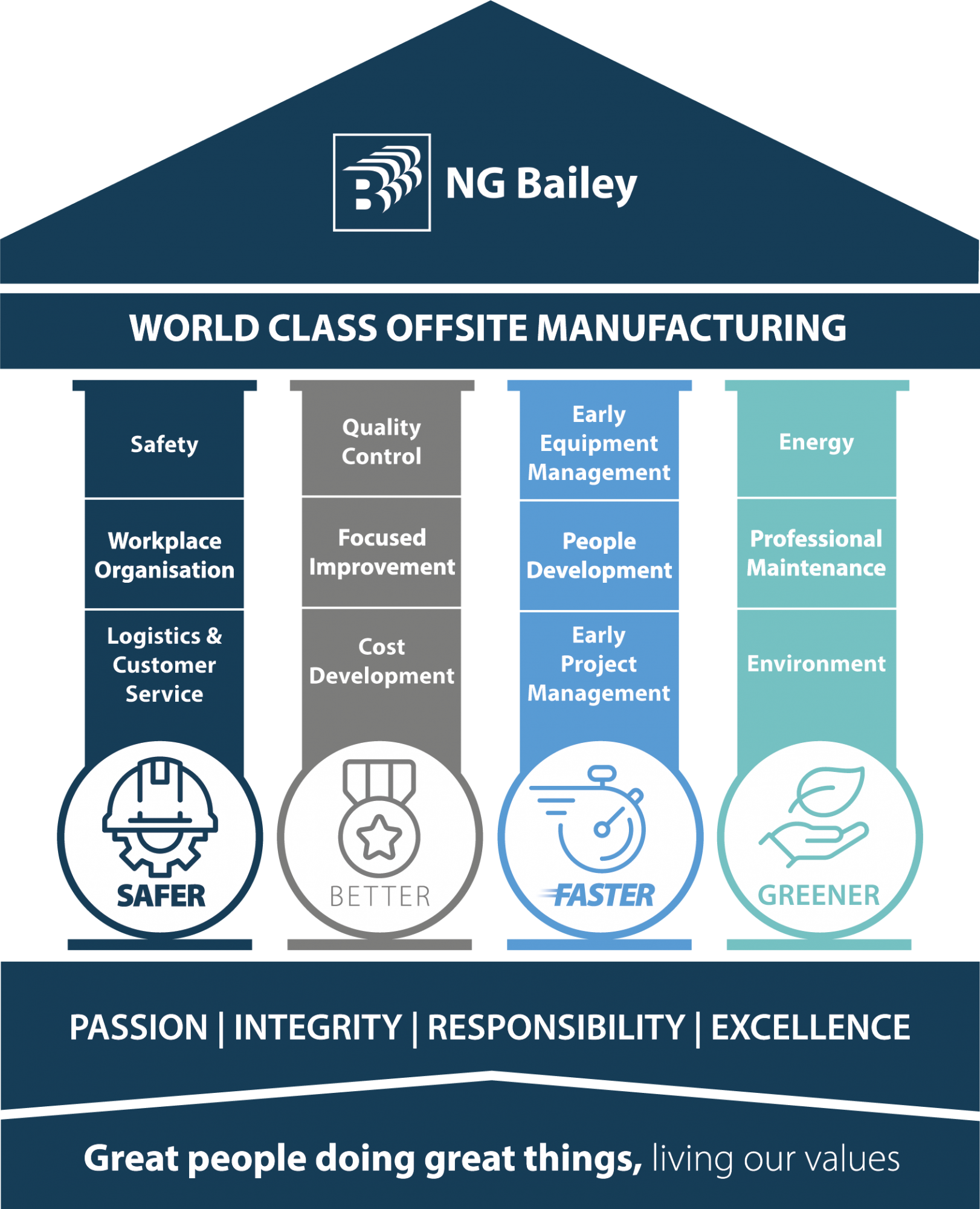
Case studies
World's First P-DfMA Building - The Forge
We're pleased to share behind-the-scenes insight into our work on The Forge; Landsec's first Net Zero Carbon development. The Forge is the world’s first Platform Design for Manufacture and Assembly (P-DfMA) office building. The production of parts at our specialist Offsite Manufacture facility in Bradford has removed 20,000 operative hours, from the project and delivered substantial carbon savings.
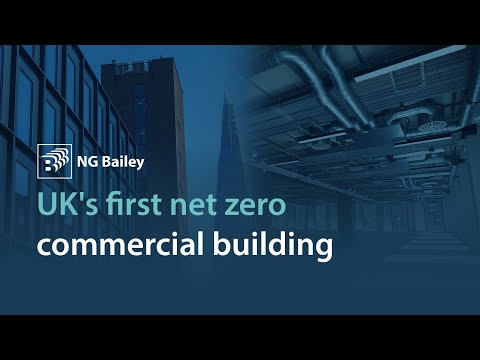
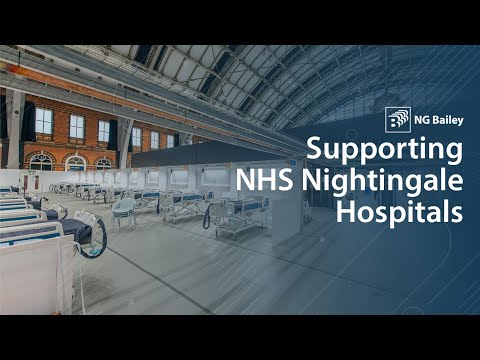
Offsite Manufacture Supporting NHS Nightingale Hospital Projects
NG Bailey Offsite Manufacture Supporting NHS Nightingale Hospital Projects. We were proud to support the fight against coronavirus by working collectively with key partners throughout the industry to create several Nightingale hospitals across the UK.
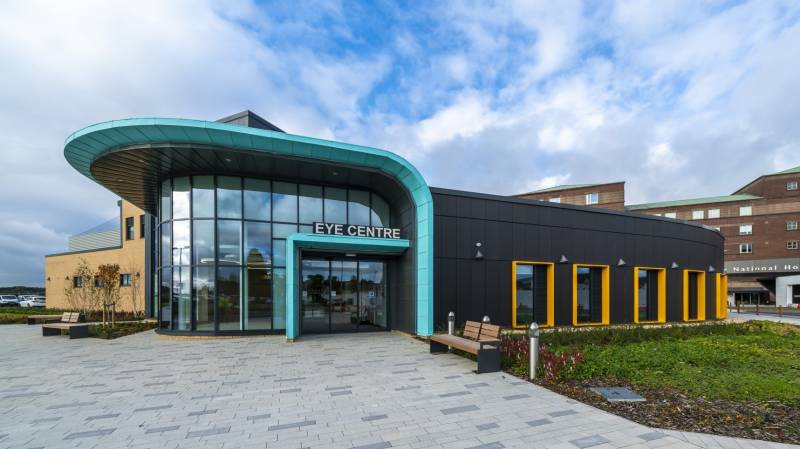
Golden Jubilee Eye Hospital
We successfully delivered the £2.9m installation of mechanical, electrical, and public health plumbing services (MEP) for a new eye care centre at the Golden Jubilee National Hospital in Clydebank, Scotland.
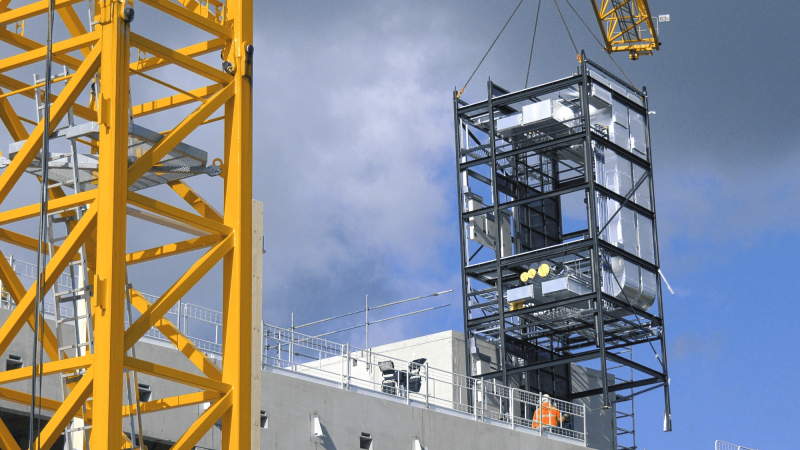
Warwick University Interdisciplinary Biomedical Research Building
The development of the Interdisciplinary Biomedical Research Building (IBRB) at the University of Warwick is an outstanding example of collaboration and modern methods of construction. The £54.3m project is being completed to world-class, industry-leading standards with at least 50% using offsite construction.
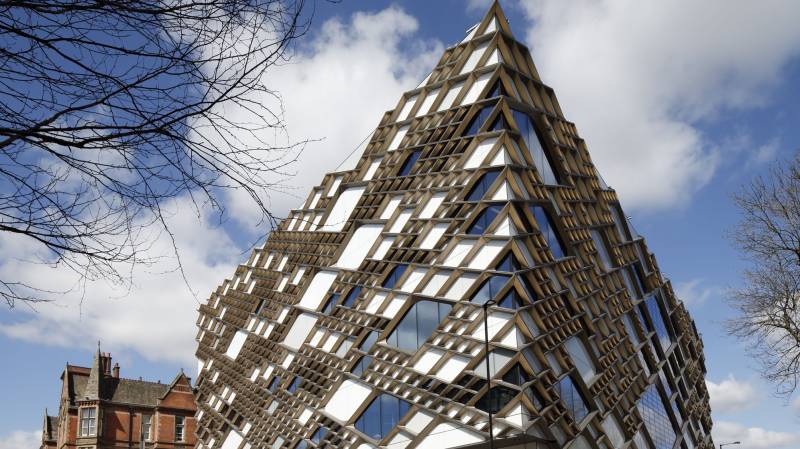
The Diamond, University of Sheffield
The Diamond is the University of Sheffield’s hub for engineering students. The iconic building houses specialist teaching facilities for engineering as well as lecture theatres, seminar rooms, a library and more than 1,000 study spaces. We delivered all mechanical and electrical installations which included a number of specialist systems such as industrial gas and ventilation services and intelligent lighting systems.
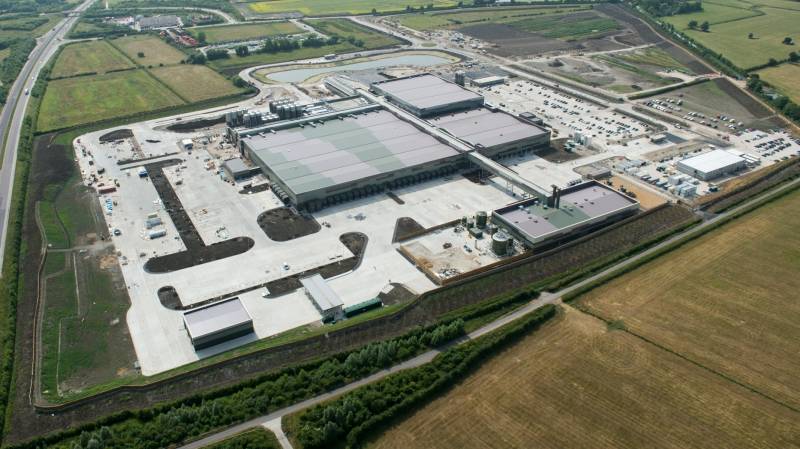
Arla Foods, Aylesbury
Arla’s £150 million flagship dairy in Aylesbury is the biggest in Europe and one of the most environmentally advanced in the world, with the capacity to process one billion litres of milk a year. We were contracted to provide all heavy industrial services associated with the mechanical and electrical work, as well as the facilities management contract, on this new processing facility built on what was farmers’ fields.
Standardisation
Standardised range of pre-engineered assemblies and products
Standard products consist of a pre-designed proven solution, utilising a kit-of-parts, in turn minimising site installation time and health and safety risks.
As an industry we are talking more about modern methods of construction and product standardisation, which presents an opportunity to further shape our existing offsite manufacturing solution.
To help us to do this, we have launched a standardised range of pre-engineered assemblies and products created by our Central Engineering and Offsite Manufacturing team that will add benefit to internal and external customers.
Get in touch
To find out more about how our Offsite Manufacturing team can support you, simply complete the form below.